Welcome to the Digital Launch Factory
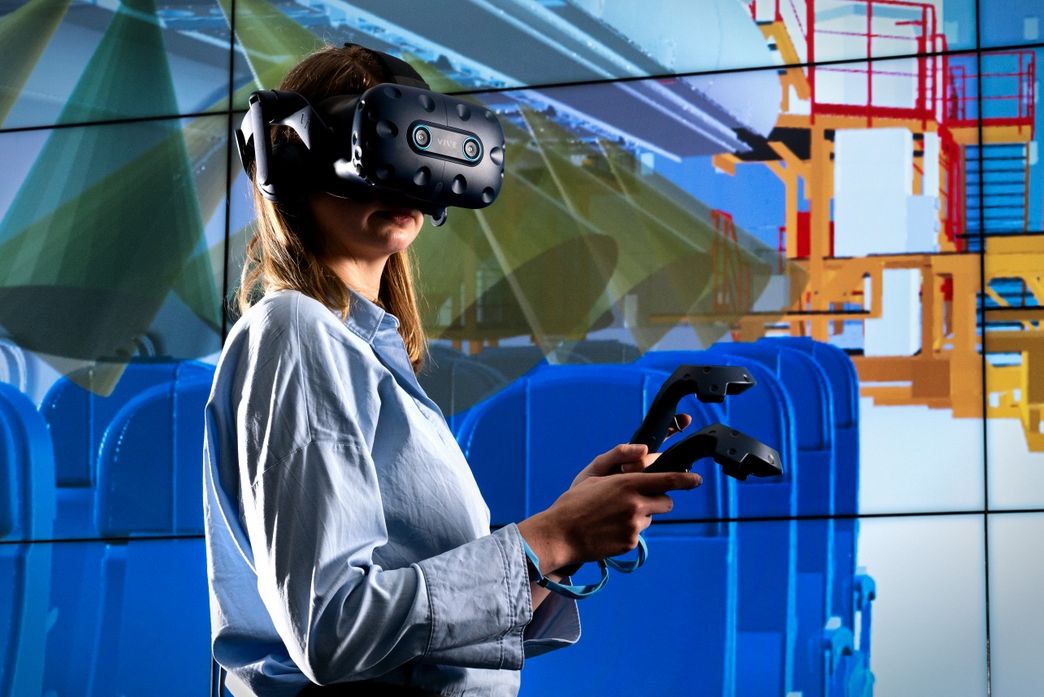
DLR and Airbus are working together to create a new airplane ‘factory’ in Hamburg where new concepts and technologies will be evaluated and tested. What makes it remarkable is that it takes up no space at all, because it is digital.
Hydrogen or synthetic kerosene? The question of which energy carrier will power future aircraft is one of the most pressing in air transport. Physical parameters such as mass, drag, energy efficiency and climate impact, all of which are important when addressing this issue in flight mechanics, are already being calculated in cooperation with DLR’s specialist institutes. However, these parameters alone do not allow predictions to be made about the actual potential of a particular technology. That also depends on how cost effectively it can be manufactured as an industrial product.
Simulations provide a glimpse into the future
It is not possible to reliably assess how complex adapting the manufacturing process for commercial aircraft to new technologies – such as modified tanks or engines – will prove to be. The manufacturing systems are far too complex for this. In addition, the requirements for industrial production processes are at least partly secret. Accordingly, researchers can only partially take these requirements into account in their work. As part of the EPSIA project, which has the goal of increasing efficiency in production planning and control using prescriptive analytics and is funded by the German Federal Ministry for Economic Affairs and Climate Action, DLR and Airbus are working together to develop a digital factory environment. In the ‘Digital Launch Factory’, DLR will act as a virtual manufacturer and evaluate the industrial viability of new aircraft.
Energy-efficient and climate-neutral
One of the targets that the German government has set for the country in line with the European Commission’s Green Deal is to effectively implement climate protection in air transport and bring the necessary technologies to a state of market readiness. Air transport is to be climate neutral and sustainable by 2050. To achieve this, aircraft shall consume only half the amount of energy that they do now. It also means that future aircraft configurations will look very different to the way they do today. In terms of the external shape, this could mean higher wingspans or new propulsion concepts. The internal structure will have to allow space for climate-neutral technologies such as hydrogen tanks, fuel cells and batteries.
DLR Institute of System Architectures in Aeronautics
DLR Institute of System Architectures in Aeronautics
In Hamburg, 60 personnel are working on making future aircraft and their components safer, more powerful and more efficient. Their research focuses on the ‘digital aircraft’, in which all the properties are represented virtually during the design, testing, manufacturing and certification process. In this process, various subsystems are coupled together to form an overall system. This combination of subsystems is referred to as a system architecture. As part of their work, the researchers look at the individual systems and the ways in which they interact.
However, climate protection does not stop with innovative aircraft concepts that call for new technologies and construction methods; the production processes themselves need to become greener, as they have important potential in the form of energy-efficient, sustainable manufacturing. With that in mind, the Digital Launch Factory team is creating simulations for the assembly of the most important aircraft components, and these can be adapted to different configurations. The calculations also show the extent to which energy and material costs can be reduced and how far it is possible to go in terms of implementing a closed material cycle. Whenever new product architectures or manufacturing processes are developed or existing ones modified, new simulations can be integrated into the virtual factory. DLR’s personnel are conducting such research as part of initiatives such as the cross-sectoral Factory of the Future project.
Agile, modular manufacturing
The Hamburg-based team is focusing on the industrial aspects that relate to Germany’s added-value contributions to air transport products today, such as the integration of the cabin and systems into the fuselage. Until now, the fuselage has been manufactured first, followed by integration of the subsystems and installation of the cabin monuments. Among other things, researchers at DLR are looking at integrating the subsystems into pre-assembled units such as the cabin crown module. This contains all of the systems and cabin components above the row of windows, including the luggage racks, ceiling panels and air conditioning ducts. The supplier delivers the prefabricated modules, thus reducing the number of components that need to be installed in the aircraft at the same time. This new method also considerably reduces the assembly time for the aircraft interior, as there is no need to wait for the fuselage to be completed. The time required for the complex alignment of the individual panel elements is also shorter. In summary, the design of the aircraft cabin has a direct impact on the production process. DLR researchers are working on designing cabins under the constraints of efficient industrialisation so that they are safe, comfortable andcustomisable. The ability to customise cabins is a key selling point for aircraft manufacturers.
But not everything is digital in the Digital Launch Factory; some aspects are actually set up in the laboratory, in collaboration with Airbus, Diehl and other industry partners at the ZAL Center of Applied Aeronautical Research in Hamburg. This includes a robot-assisted pre-assembly station, where experts test how collaborative robots can automatically install the subsystems in the assembly modules. They feed their findings directly into the algorithms of the digitalised factory. This is the first step towards Industry 4.0, where the real and virtual worlds will be networked together. Assemblies like the crown module can initially be built using automation through joint projects with Europe’s largest aircraft manufacturers. Processes can then be scaled up for full production using the virtual factory. Pre-assembly in real life is vital in order to allow researchers to validate the digital factory using these data.
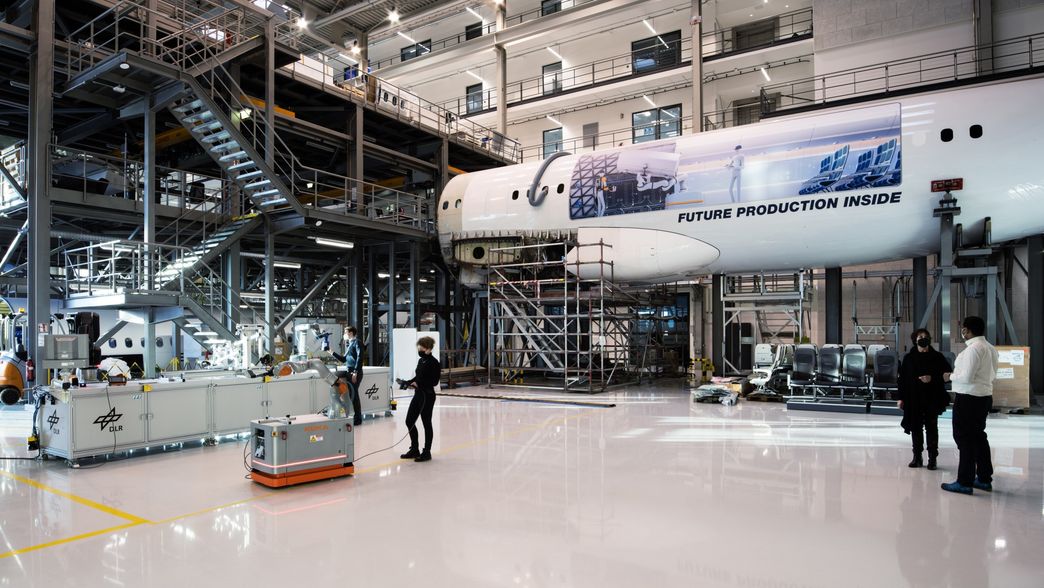
Mutual exchange throughout the lifecycle
Another goal of the Digital Launch Factory is to connect experts in areas ranging from design through to production. Co-design is an approach whereby the design and production of a product are both taken into consideration during all phases of development. This minimises costly reworking of the product design during the production phase. In addition, this method also looks at manufacturing aspects already during the design of new aircraft configurations. The benefits of co-design are such that this is a key area of focus for research in the German aviation industry. Data, models and tools will be used more consistently as part of digitalisation.
The Digital Launch Factory is a key building block that DLR can use to model and study aviation as an overall system. Revolutionary changes such as climate-neutral flight can only be implemented efficiently if design, industrialisation and operations are synergistically coordinated. For the researchers in Hamburg, the first step is to get all of the key DLR institutes and industry partners around the table, so that together they can closely examine the interactions between the aircraft as a product and its manufacturing process.
Author: Björn Nagel (Founding Director of the DLR Institute of System Architectures in Aeronautics)
This article first appeared in DLRmagazin 170 of the German Aerospace Center.